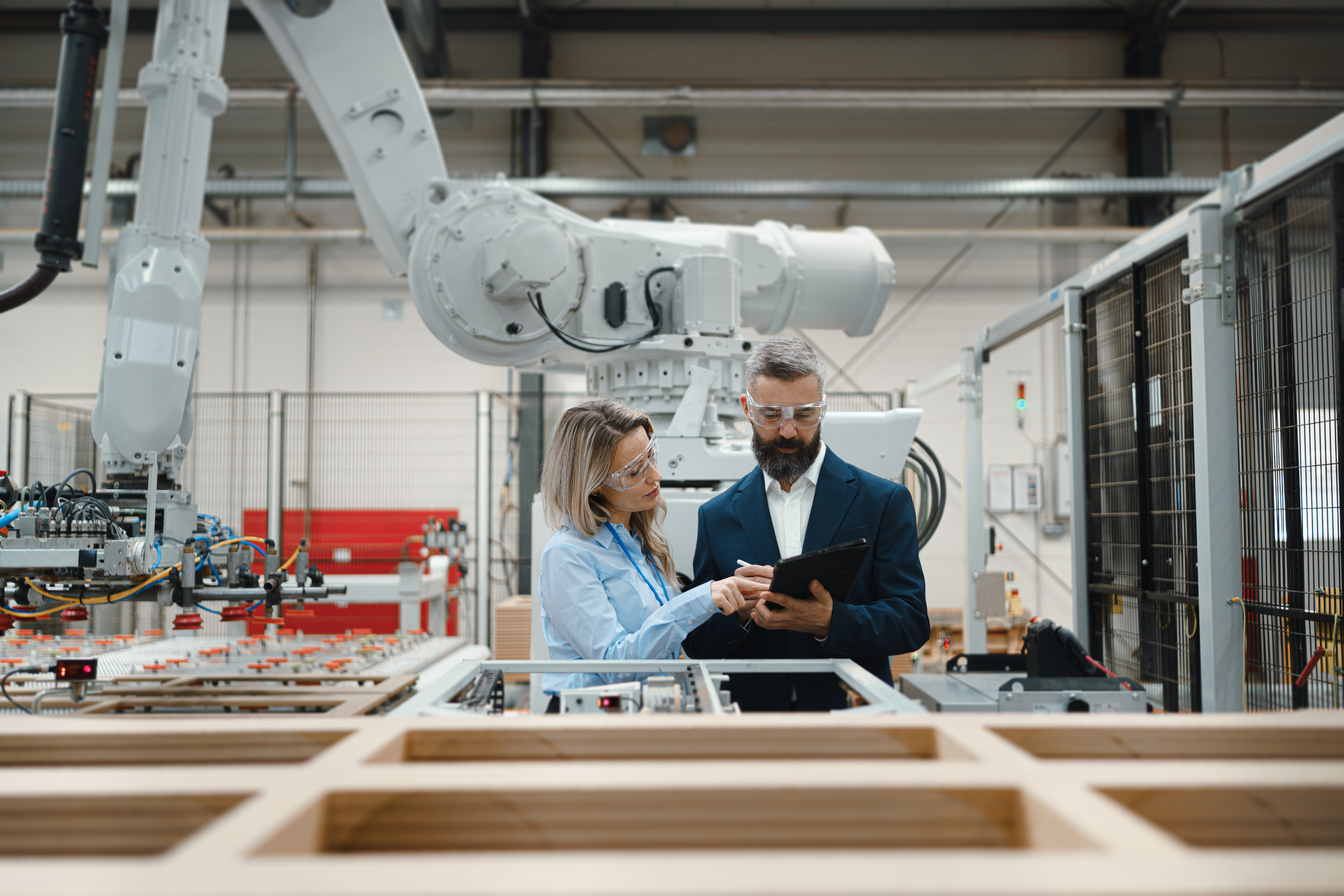
Product recalls cost companies around $10 million in direct expenses alone. For manufacturers, this financial reality makes lot tracking software more than just a compliance tool—it’s become essential protection against devastating business disruption.
Lot tracking assigns unique identifiers to product batches, creating precise traceability from raw materials through production to final delivery. The stakes are high: the Food Safety Modernization Act grants the FDA broad authority to mandate recalls and shut down operations if companies cannot demonstrate proper lot tracking data collection and management.
The impact extends beyond regulatory compliance. Lot tracking is particularly critical in food, pharmaceuticals, automotive, and aviation, where even minor inconsistencies can threaten human health and safety. Your tracking system protects more than operational efficiency—it safeguards your customers, your reputation, and your bottom line.
But how do you choose the right solution? Many manufacturers struggle with this decision, unsure which features matter most or how to evaluate software against their specific operational needs.
This guide provides a practical roadmap for selecting lot tracking software that fits your manufacturing operation. You’ll learn to identify essential features, evaluate vendor options, and plan implementation that strengthens both quality control and compliance capabilities.
Understand What Lot Tracking Software Does
Lot tracking forms the backbone of product traceability in manufacturing operations. Before evaluating software options, you need to understand what this process accomplishes and how technology has changed the game.
What is lot tracking in manufacturing?
Lot tracking is a systematic method of monitoring specific batches or groups of products throughout their entire lifecycle. These batches, called “lots,” consist of items manufactured under identical conditions, using the same raw materials during a single production run.
Each lot receives a unique identifier that connects it to critical information:
- Production and expiration dates
- Supplier details and origins
- Quality control results
- Manufacturing conditions
- Distribution history
This process creates a complete record of every component and finished product in your organization. A food manufacturer might assign lot numbers to batches of canned goods to trace ingredients back to suppliers or manage expiration dates. The system supports inventory management strategies like FIFO (First-In, First-Out) or FEFO (First-Expired, First-Out), ensuring older stock moves first to reduce waste.
What you get is a digital paper trail that follows products from raw materials to end consumers.
How software automates the tracking process
Modern lot tracking software transforms what was once a complex, paper-based workflow into a streamlined operation. These systems do much more than simple record-keeping.
Properly implemented lot tracking software:
- Creates and assigns unique lot numbers automatically
- Captures lot data through barcode scanners or RFID tags to eliminate manual entry
- Records every movement and transaction in real-time
- Maintains complete genealogy or “family trees” of products
- Generates instant traceability reports both upstream and downstream
The technology works by recording transactions at every critical point. When receiving raw materials, an employee scans an automatically generated label that identifies the specific lot. During production and shipping, the system tracks each component’s movement without paperwork.
These systems integrate with enterprise solutions like ERP and inventory management platforms to create a single source of truth for all product data. This integration enables bidirectional traceability—following products forward to customers or backward to raw material sources.
Why manual tracking is no longer enough
Some businesses still track lots manually using paper records or spreadsheets, but this approach presents significant limitations in today’s manufacturing environment.
Manual tracking systems create several problems:
- Human error: Small mistakes in data entry can cascade into massive problems
- Time consumption: Manually recording lot information at each handling point is extremely slow
- Limited visibility: Paper systems can’t provide real-time information about inventory status
- Audit challenges: Finding specific lot information during inspections or recalls becomes time-consuming
- Scalability issues: As production volumes increase, manual systems quickly become unmanageable
The bottom line: if an audit or recall occurs, manual tracking can take hours or days to trace where materials are in production or in the supply chain. Automated systems provide instant access to this information, potentially saving millions in recall costs and protecting consumer safety.
Regulatory requirements in many industries have become increasingly stringent, making compliance through manual systems nearly impossible. Automated lot tracking software ensures you can meet these demands with accurate, accessible records that satisfy auditors and regulatory bodies.
Identify Your Business Needs
Successful lot tracking implementation starts with understanding your specific operational requirements. Your software choice must align with your manufacturing challenges, regulatory obligations, and business scale. This assessment determines whether you invest in the right solution or end up with expensive software that doesn’t solve your actual problems.
Assess your current inventory challenges
Inventory management difficulties often reveal the need for robust lot tracking capabilities. Medical device manufacturers typically maintain 150 days of inventory in the field, with some companies holding up to 400 days’ worth of products. This inventory spread creates tracking, compliance, and quality control challenges that manual systems simply cannot handle.
Your lot tracking software should address these common operational problems:
- Inconsistent tracking: Manual procedures across different software and spreadsheets increase errors and waste time
- Warehouse disorganization: Poor storage practices expose inventory to damage, theft, or contamination
- Inaccurate data: Without real-time inventory visibility, businesses struggle with stockouts or overstocking, with global excess inventory costing over $250 billion annually
- Expiration management: Products approaching expiration dates need systematic tracking to implement FIFO (First-In, First-Out) or FEFO (First-Expired, First-Out) methods
Poor inventory management costs businesses an estimated $1.77 trillion globally each year. Identifying which of these challenges affects your operation most severely helps prioritize essential software features.
Consider industry-specific compliance requirements
Regulatory compliance requirements vary significantly across industries, making them crucial considerations when selecting lot tracking software. Manufacturers in food and beverage, electronics, and pharmaceuticals are legally required to maintain accurate lot-tracking records as part of their compliance processes.
The Food Traceability Rule requires documentation of traceability lot codes and sources, enabling FDA to identify food sources faster during outbreak investigations. Medical device manufacturers must comply with FDA labeling regulations or risk enforcement actions, market access delays, or patient harm.
Your lot tracking solution should align with specific regulations for your industry:
- Food manufacturers: FDA or USDA regulations depending on products manufactured
- Medical suppliers: FDA requirements for complete visibility and control over supply chain
- Pharmaceuticals: Good Manufacturing Practices (GMP) as outlined by FDA
- Aviation/automotive: Industry-specific traceability standards
Determine the scale and complexity of your operations
Manufacturing operation size and complexity significantly impact your lot tracking software requirements. Companies with multiple locations or complex supply chains need solutions that handle data across various sites and integrate with existing systems.
Consider these operational factors:
- Supply chain complexity: Global supply chains shift daily, requiring flexibility in inventory planning
- Multi-location tracking: Managing inventory data scattered across various locations presents unique challenges without unified systems
- Integration needs: Your lot tracking software should integrate with existing business process platforms to scale and support complex logistics
- Growth projections: Consider where your business will be in five or ten years and build an inventory strategy that accounts for long-term growth
Small operations might succeed with basic lot tracking features. Larger manufacturers often require advanced functionality like real-time analytics, multi-site coordination, and extensive integration capabilities.
Evaluating inventory challenges, compliance requirements, and operational scale creates a clear picture of your lot tracking software needs. This assessment serves as your roadmap through the selection process, ensuring you choose a solution that addresses your specific requirements rather than unnecessary features.
Evaluate Key Features to Look For
Once you’ve identified your business requirements, focus on specific software capabilities that deliver measurable value. The right feature set depends on your operational complexity, but certain core functions are essential for effective lot tracking.
Lot creation and traceability
Your software must automatically generate unique identifiers for each product batch while storing critical information—production dates, expiration dates, and batch numbers. Look for systems that maintain comprehensive traceability both upstream to raw material sources and downstream to customer deliveries. Advanced systems trace suspected products across all processes, from vendor delivery through production to customer shipments, generating bidirectional traceability reports.
Barcode and RFID support
Data capture technology determines how efficiently your team can record lot information. Barcode systems provide cost-effective solutions with customizable labels storing up to 7000 characters. RFID technology offers contactless functionality that reduces manual entry errors. RFID readers scan multiple tags simultaneously without line-of-sight requirements, speeding up asset audits and reducing tracking time. Your choice depends on scanning needs, environmental factors, and budget constraints.
Integration with ERP and inventory systems
Your lot tracking software should connect seamlessly with existing enterprise resource planning (ERP) and inventory management systems. This connectivity enables automatic data flow across your organization, supporting better decision-making and automating processes beyond basic inventory management. Prioritize solutions that integrate with manufacturing systems to enhance traceability and connect with accounting and e-commerce platforms, creating a single source of truth for all product data.
Real-time tracking and reporting
Real-time visibility into inventory movements and status forms the foundation of effective lot tracking. The software should provide instant access to lot histories, locations, and status changes. Reporting capabilities must support both operational decisions and compliance requirements, including the ability to generate customized recall letters that limit recall scope to specific lots.
Compliance and audit readiness
Your lot tracking software should simplify regulatory compliance through automatic documentation and audit trails. The system must support industry-specific regulations like FDA requirements, HACCP, FSMA, or ISO standards. Look for features that automate expiration alerts, enable batch separation protocols, and generate compliance reports for audits. Quality solutions reduce audit preparation time by maintaining complete histories from production to delivery.
What features matter most? That depends on your specific manufacturing environment, but these five categories form the foundation of any effective lot tracking system.
Compare and Shortlist Software Options
Your requirements are clear, and you understand the essential features. Now comes the critical evaluation phase—comparing available lot tracking solutions to find the right fit for your manufacturing operation.
Create a feature checklist
Start with a comprehensive checklist that reflects your specific needs. Your evaluation framework should cover:
- Essential functionality: Lot creation, traceability, barcode/RFID support, and reporting capabilities
- Integration needs: Compatibility with existing ERP, supply chain, and warehouse systems
- User interface: Ease of navigation and operation for all technical skill levels
- Data security: Authentication, access levels, encryption, and backup protocols
Mark features as “must-have” versus “nice-to-have” based on your manufacturing priorities. This distinction prevents feature creep from driving your decision.
Review vendor reputation and support
Due diligence on vendors can save significant headaches later. Research how long they’ve been in business and whether they’re experiencing growth or decline. Customer service quality matters—verify their support team can handle your questions and concerns effectively.
Read user reviews on independent platforms like Capterra, Trustpilot, and specialized app stores. Focus on feedback about support responsiveness, system reliability, and implementation experiences. Pay particular attention to reviews from companies similar to yours in size and industry.
Request demos and trials
Hands-on evaluation provides insights no sales presentation can match. Most vendors offer free trials, typically 14 days, to test software usability and functionality. Use this time strategically—test all critical features and involve your actual end-users in the evaluation process.
Establish clear performance indicators to measure whether the implementation meets your expectations. Document what works well and what doesn’t during the trial period.
Check for scalability and customization
Your software choice should grow with your business. Look for solutions offering different upgrade levels and additional modules as your requirements change. Verify the software can handle more users and increased data volumes without performance issues.
Consider whether customization options align with your specific manufacturing processes and industry regulations. The right solution adapts to your workflow rather than forcing you to adapt to the software.
Plan for Implementation and Training
Getting your lot tracking software selected is only the beginning. The real work starts with implementation, and this phase determines whether your investment delivers the expected returns.
Prepare your data and inventory records
Start with lot number standardization. Whether you choose date-based codes or alphanumeric sequences, consistency matters for smooth operations. A lot number like “20250115-001” represents production date (Jan 15, 2025) plus a batch identifier—clear and systematic.
Before migration, organize your existing records. Production dates, expiration dates, supplier information, and quality control results need to be accurate and complete. Your lot tracking system should integrate with current inventory management solutions to maintain data synchronization across platforms. This alignment ensures lot information matches stock levels, order fulfillment, and production schedules.
Train your team on new workflows
The most sophisticated lot tracking system fails without proper staff training. Everyone from warehouse staff to customer service needs to understand how to assign, track, and reference lot numbers.
Develop training programs that cover proper handling, labeling, and recordkeeping procedures. Customize materials to fit your specific implementation—you know your teams best. This investment in training builds a competent workforce ready to execute your inventory management strategy effectively.
Set up backup and data recovery protocols
Protect your lot tracking data with robust backup procedures. Establish backup frequencies aligned with your recovery point objectives. If your RPO is 15 minutes, schedule backups at least that often.
Test your recovery capabilities regularly by restoring backups in non-production environments. Document restoration steps clearly and train teams to execute them during system failures. Implement automated consistency checks after each backup to validate data integrity.
Monitor performance post-implementation
Once your system launches, evaluate its effectiveness through data analysis and employee feedback. Look for opportunities to improve traceability, efficiency, and error reduction.
Your manufacturing organization will evolve, and your lot tracking processes should evolve with it. Continue refining procedures to maintain alignment with changing business requirements.
Conclusion
Choosing lot tracking software isn’t just a technology decision—it’s a strategic investment in your manufacturing operation’s future. The right system protects your bottom line while positioning your company for sustainable growth.
The selection process requires methodical evaluation of your specific needs. Companies that rush this decision often find themselves with software that doesn’t match their operational requirements or compliance obligations. Take time to assess your inventory challenges, regulatory demands, and operational scale before evaluating vendors.
Your software choice should align with your manufacturing reality. Look for systems that integrate seamlessly with existing operations, provide real-time visibility, and support your compliance requirements. The best solution grows with your business rather than limiting your expansion options.
Implementation planning determines success. Even sophisticated software fails without proper data preparation, staff training, and ongoing performance monitoring. Companies that invest in thorough implementation see faster adoption and better results.
The bottom line: lot tracking software transforms from a compliance necessity into a competitive advantage. Manufacturers with precise traceability respond faster to quality issues, maintain tighter inventory control, and build stronger customer relationships. Your investment protects more than regulatory compliance—it safeguards your reputation and market position.
Start your selection process with clear requirements and realistic timelines. The effort invested in choosing the right solution pays dividends through reduced risk and improved operational performance for years to come.
Key Takeaways
Choosing the right lot tracking software is crucial for manufacturers to avoid costly recalls, maintain compliance, and protect their reputation while streamlining operations.
• Assess your specific needs first: Evaluate current inventory challenges, industry compliance requirements, and operational scale before comparing software options to ensure the solution fits your unique manufacturing environment.
• Prioritize essential features: Focus on lot creation/traceability, barcode/RFID support, ERP integration, real-time tracking, and compliance reporting capabilities that align with your business requirements.
• Test before committing: Request demos and free trials to evaluate usability with actual end-users, while checking vendor reputation, support quality, and scalability options.
• Plan implementation thoroughly: Prepare data migration, standardize lot numbering formats, train staff on new workflows, and establish backup protocols to ensure successful system deployment.
• Monitor post-implementation performance: Regularly evaluate system effectiveness through data analysis and employee feedback to optimize processes and maintain alignment with evolving business needs.
The right lot tracking software transforms from a compliance necessity into a competitive advantage, delivering operational efficiency, quality control, and significant cost savings through reduced waste and recall prevention.
FAQs
Q1. What is lot tracking software and why is it important for manufacturers? Lot tracking software is a system that allows manufacturers to create and maintain detailed records of raw materials and finished products, organized by batches or lots. It’s crucial for quality control, regulatory compliance, and efficient recall management, helping manufacturers avoid costly errors and protect their reputation.
Q2. What key features should I look for in lot tracking software? Essential features include lot creation and traceability, barcode or RFID support, integration with existing ERP systems, real-time tracking and reporting capabilities, and compliance-ready functionalities. The software should also be scalable and customizable to fit your specific manufacturing needs.
Q3. How does lot tracking software improve inventory management? Lot tracking software provides real-time visibility into inventory movements and status, enabling better decision-making and reducing issues like stockouts or overstocking. It supports strategies like FIFO (First-In, First-Out) or FEFO (First-Expired, First-Out), helping to minimize waste and optimize inventory control.
Q4. What steps should I take to implement lot tracking software successfully? Successful implementation involves preparing your data and inventory records, standardizing lot number formats, thoroughly training your team on new workflows, setting up robust backup and data recovery protocols, and continuously monitoring performance post-implementation to ensure the system meets your evolving needs.
Q5. How can lot tracking software help with regulatory compliance? Lot tracking software simplifies regulatory compliance by automating documentation and maintaining detailed audit trails. It supports industry-specific regulations like FDA requirements, HACCP, FSMA, or ISO standards. The software can generate compliance reports, automate expiration alerts, and enable batch separation protocols, significantly reducing audit preparation time.